Simufact Additive : Additive manufacturing simulation
Simufact Additive is a powerful and scalable software solution for the simulation of metal-based Additive Manufacturing (AM) processes.
Properly, Simufact Additive is an easy-to-use software technology allowing to quickly predict the quality of fabrication of additively manufactured metal parts. The user interface is intuitive enough to allow the setup of an analysis in a few minutes. With a material database of the most used metals for additive manufacturing, it is possible to simulate the additive process for part made of aluminum, stainless steel, titanium, and others.
Moreover, Simufact Additive covers the simulation of Powder Bed Fusion processes, e.g., known as:
- Selective Laser Melting (SLM)
- Direct Metal Laser Sintering (DMLS) – an EOS technology
- LaserCUSING® – a Concept Laser technology
Simufact Additive
Benefits
Based on the MARC solver robustness, Simufact Additive allows leveraging the best-in-class additive manufacturing simulation technology to:
- Calculate part distortion during printing and after cooling and after separation from the base
- Automatically compensate the distortion to obtain for perfect parts
- Calculate and minimize residual stresses
- Design and optimize support structures
- Analyze effects of positioning on the base plate
- Predict manufacturing issues such as re-coat contact, cracks, or layer offset
- Quickly compare results between as designed and as manufactured with best fit capabilities
- Simulate the process of Hot Isostatic Pressure (HIP) to analyze relative density
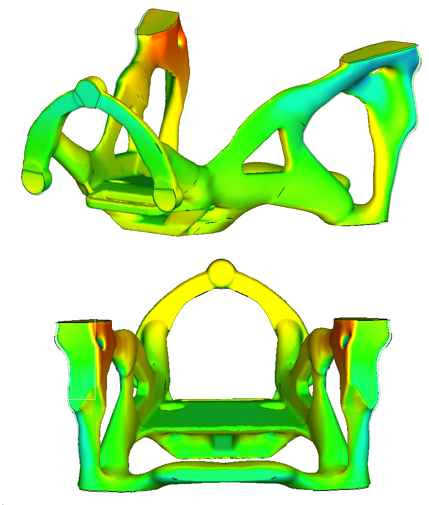
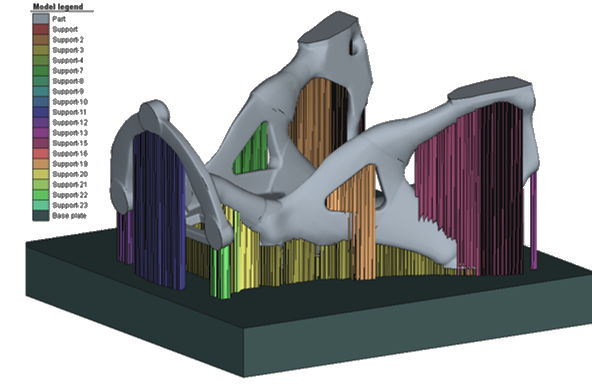
Simufact Additive
Features
Simufact Additive offers three different calculation methods to address the required accuracy vs. speed for each additive manufacturing simulation project:
- To achieve practical results more quickly, the “inherent strain” method was implemented to additive production in the powder bed when developing the software.
- This method has been proven to achieve excellent results in terms of distortion behaviour and calculation of internal stresses. It is, therefore, the first choice for achieving practical results quickly, i.e., within minutes or a few hours.
- An automatic calibration process is implemented to evaluate inherent strains values easily.
- Used for specific manufacturing problems that require an insight into the temperature processes, e.g., to set heat dissipating support structures or to evaluate the effect of a build plate heating system.
- The thermo-mechanical simulation is suitable if mechanical and thermal results are to be represented in a simulation. Besides, better prediction results can be achieved in special manufacturing situations than with the purely mechanical inherent strains.