It is an exciting time for Industrial Equipment Engineering! Since the first industrial revolution, the product’s features and especially the mechanical performances were the focus points of manufacturers. However today quality and features are not enough anymore, for both OEM and their customers.
Globally, three megatrends are transforming the way Industrial Equipment manufacturers are thinking about their business from external interactions (customers, distribution, service centres, suppliers) to internal processes including sales, engineering, and manufacturing.
Ultimately these trends are tightly related and converging to the same objective of providing value by delivering superior customer experiences.
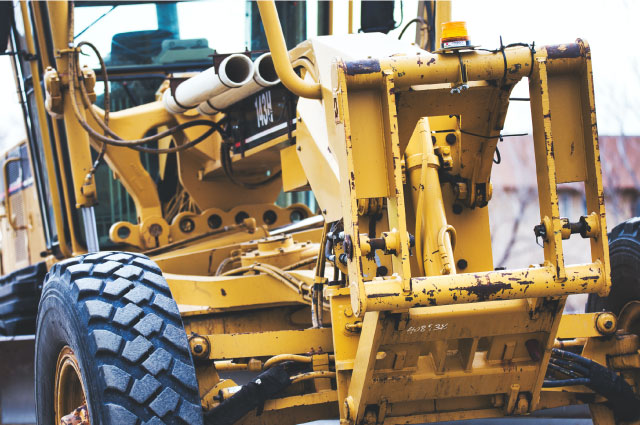
Although its adoption is slower than forecasted by analysts all over the Globe, the Internet of Things (IoT), has passed the stage of ‘buzz word’ and it is in every strategic plan. Nevertheless, few companies realize the huge impacts such implementation may generate. At the product development level, the IoT introduces a new level of complexity, often outside the core competencies. The combination and overlap of multiple disciplines such as mechanics, software development and electronics are exponentially challenging the product development cycles and quality control. Without adequate methodologies and tools, it is virtually impossible to satisfy customer requirements in time and on budget.
Nobody will buy your products anymore! Compressed air as a service, Lighting as a Service, filtered air as a Service, Power as a Service…these are just a few examples of new business models proposed by industrial manufacturers that deployed a Product as a Service strategy. In the consumer goods arena, this engagement has been already reality for years, whereas in this industry it still has a great growth potential and could unlock new revenues/high margin opportunities.
Also referred to as one-of-the-kind Design and Production or Production of One.
In a nutshell, mass customization is the concept of achieving both customization and scale of economy (B. Joseph Pine II, 1999). In the current economy of experience, this definition is not enough as time to market and no compromise on quality, are key factors. Mass customization is not new, although for Industrial Equipment engineering, often mass customization may be confused with lean manufacturing and Just-in-Time strategies or batch production.
Industrial Equipment
What we do
Your business transformation goes beyond the implementation of the newest technologies. At Optimec is all about our customers and our customers’ customers. Our engagement is strictly based on the creation of value, aligning your objectives while addressing current industrial equipment challenges.
Technology is nothing but an enabler; By itself it will not solve your challenges. At Optimec, we believe that People – Tools – Processes must equally be considered and addressed, to address industries challenges.
Optimec help validate and optimize industrial products or manufacturing tooling.
- For stationary or moving equipment, we help leverages the engineering simulation technologies (FEA, CFD) to make sure the products will perform as intended in terms of structural, thermal and vibration requirements.
- Before producing any expensive tooling to manufacture parts, we help to validate the forming and assembly processes of parts, both to study the parts final shape and assess the stresses in tooling itself.
Moreover, at Optimec, we provide help to implement PLM solutions to help realize the digital transformation, to streamline the different processes involved in new product development.
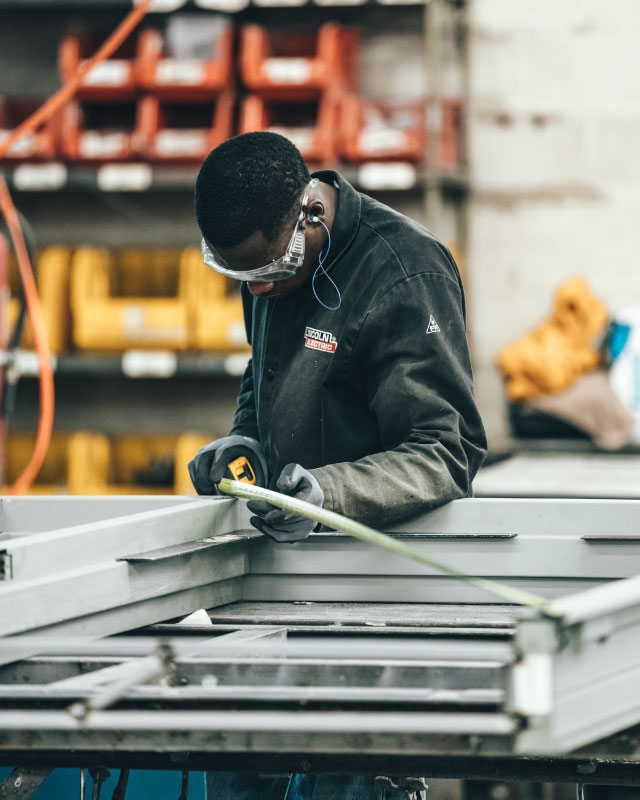
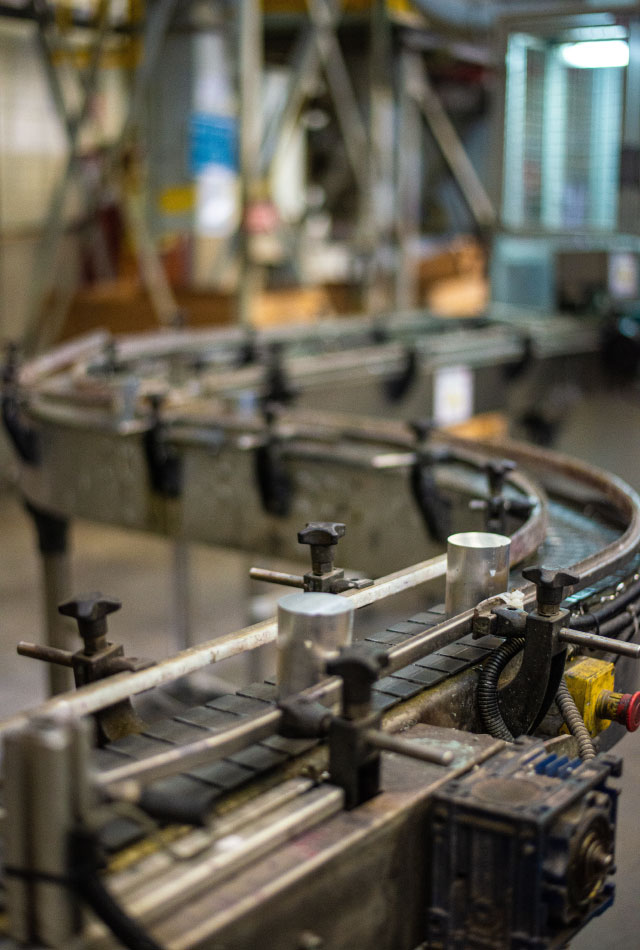
Industrial Equipment
How we do
To address the challenges of engineering industrial equipment products, Optimec intervene on the simulation side validating product performance at the design level, and at the manufacturing level.
At the design level, Optimec realizes static, dynamic, and thermal analyses using SIMULIA ABAQUS to optimize product behaviour and quality with realistic simulations. Validating your product virtually with high-end technology allows eliminating design problems once the products hit the market.
For complex products containing mechanisms like robots, MSC ADAMS is used to simulate the dynamic behaviour, capture loads, and verify collisions.
On the manufacturing side, Optimec can generate organically optimized design for parts to be manufactured by additive manufacturing technologies using TOSCA technology. Additively manufactured parts create significant problems of distortion and residual stresses due to constant heating and cooling during manufacturing. Using SIMUFACT ADDITIVE, Optimec simulates the manufacturing process to ensure quality production by optimizing support positions and part orientation.
If metal parts are to be manufactured by sheet forming or forging, Optimec leverages SIMUFACT FORMING technology to simulate and validate the forming process before cutting and metal for tooling. Optimec can thus validate material flow, thicknesses, spring back and solve die crack problems.