THE NEXT INDUSTRY REVOLUTION IN TRANSPORT AND MOBILITY
For more than a century, the Transport & Mobility (T&M) industry has evolved around one single theme: develop, manufacture, and maintain a vehicle, mainly powered by fossil combustibles, and meant to be acquired and operated by an owner.
This is not limited to cars but extended to the entire transport and mobility industry including Truck and Buses, Motorcycles, Trains and all means of ground transportation.
This paradigm has changed and continues to mutate under the pressure of new generations’ habits and lifestyle. The impact on manufacturers and their ecosystem is enormous. This transformation is allowing the positioning of new players that, in only a five-year period, could successfully penetrate an historically closed industry, setting the new rules and initiating a chain reaction of innovations.
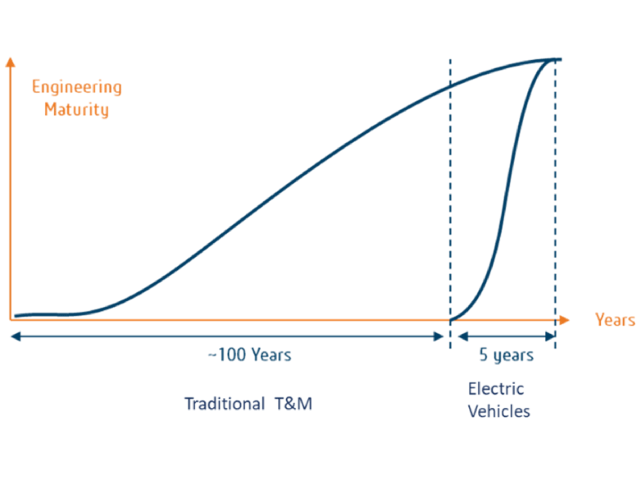
Moving from gasoline (or other combustible) to electric impacts the whole architecture and technologies of the vehicles, pushing to reengineer completely and do it fast!
Manufactures have to deal with a panoply of interdependency of systems such as batteries, HVAC, info entertainment, sensors, power electronics, powertrain that will ultimately affect the mechanical structure, body concepts and design.
Embedded software and infrastructure (gateways and antennae) ensuring connectivity are also integrating the development and manufacturing cycles.
Thus, new environment and more complexity are challenging the current state of mechanical centric development. For example, how an antenna electromagnetic fields will be interfering with other fields onboard systems and passengers?
In a nutshell, mass customization is the concept of achieving both customization and scale of economy (B. Joseph Pine II, 1999). In the current economy of experience, this definition is not enough as time to market and importance of quality are key factors.
In the experience economy, the crucial point is that the OEM could trigger and adjust the business processes based on its unique customer’s requirements (Push), from sales, procurement to engineering and manufacturing.
Because of continuously increasing product complexity, product variants and production variables, lead time and quality may be seriously challenged. Inadequate tools and manual processes will not be able to support the change. Processes will need to be digitized or, even better, automated and enhanced by artificial intelligence and integrated. A modern platform should enable the flow of information (Digital Thread), throughout the entire lifecycle of the product, from order to service.
In order to support fast development times and high quality, adoption of simulation technologies is critical. It minimizes costly physical tests and validates the interoperability of systems before any manufacturing takes place.
Quality, regulations and cost (QRC) are the elements of the equation that OEM in transportation and mobility, have to constantly solve by finding the right balance. From crash testing, to recyclability, recalls and now autonomous vehicles, complexity is just growing . Across the globe, governments are becoming stricter than ever on safety, emissions and recyclability. Not complying with legislation can result in very harsh penalties. Additionally, cities are simply banning — or will soon ban — vehicles that do not meet their own standards.
Transport and Mobility
What we do
We believe in the digital simulation of products in all stages of development and service, as well as the digitalization and automation of all the processes supporting the entire Product Lifecycle Management
Optimec has experience in many ground transportation engineering projects, and here are some examples of what we do.
- We contribute to validating and optimizing mechanical designs under varied requirements. For example, building simulation models of full-vehicle body structure of cars, trucks, or buses for static and stiffness studies, or for rollover and crash analyses.
- We validate simulation results with physical tests. To do that, we work in close relationship with a local crash test centre.
- We help customers validate electronic components, electric motors and battery packs for random vibration, shock loading, and fatigue requirements.
- We validate the required standard tests beforehand, preventing failed physical tests for complete vehicle simulations to smaller assembly analyses like seats pulling tests.
Using the latest CAE technology, loads have become the biggest unknown information for engineering simulations. At Optimec, we use Multibody Dynamics tools to realize vehicle ride simulations extracting load histories for fatigue analysis.
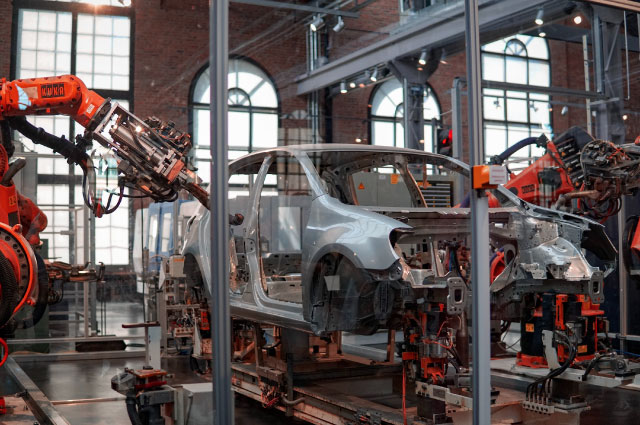
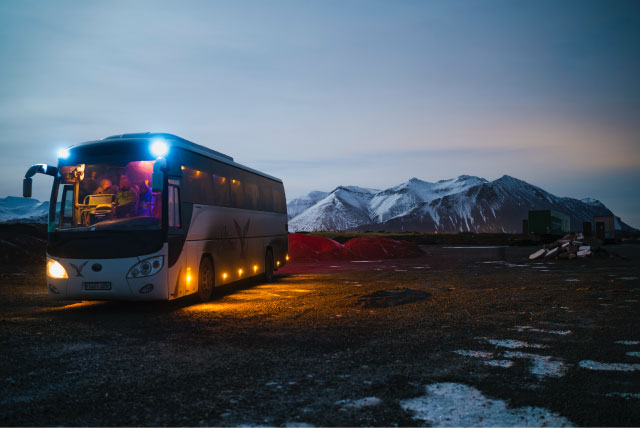
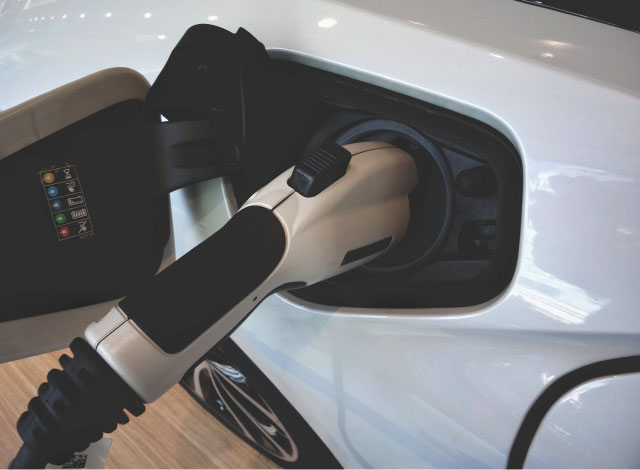
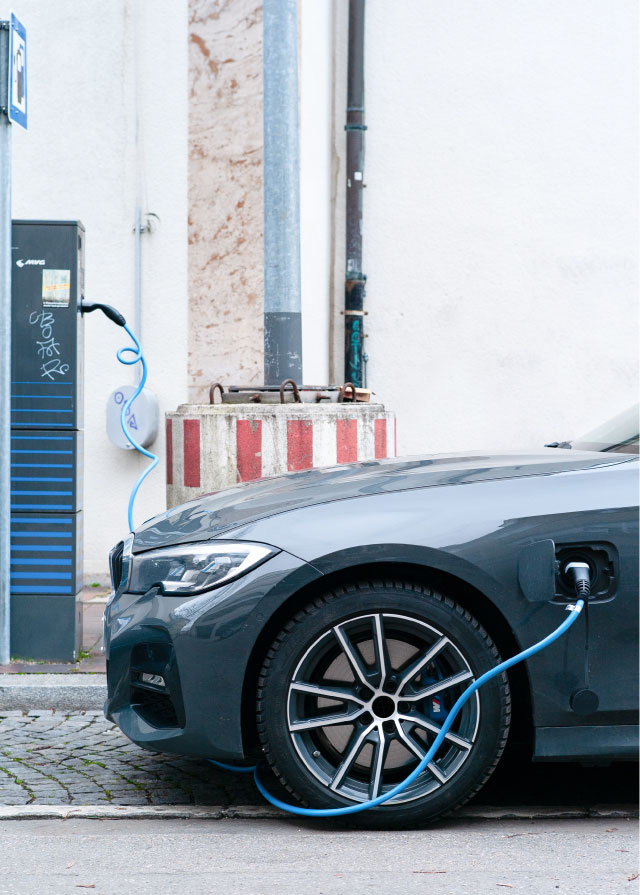
Transport and Mobility
How we do
Optimec Consultants intervene at different stages to support new product development for ground transportation and mobility projects.
On the PLM side, Optimec implements and supports modern processes within the 3DEXPERIENCE platform leveraging ENOVIA technology.
On the engineering simulation side, Optimec virtually validates ground transportation products from design to manufacturing. Examples of involvement at an early stage of design includes handling and load analysis of vehicle using multibody dynamics (MBD) tool MSC ADAMS, and topology optimization also known as generative design using SIMULIA TOSCA.
During product development, stress, vibration, and thermal analyses are performed using SIMULIA ABAQUS to validate product performance, while design of experiments (DoE) and optimization using ISIGHT are sometimes used to broaden the analysis range.
With the importance of vehicle efficiency, Optimec uses CFD analyses with either PowerFlow or 3DEXPERIENCE to evaluate drag and HVAC performance pushing optimization and innovation.
Once the design is matured enough, fatigue analyses using FE-SAFE is usually done to verify fatigue life and thus ensure the quality of new products.
Down the line, when physical prototypes are built, Optimec supports experimental test using strain gauges to validate structure integrity and reverse calculate the real dynamic loads using TRUE LOAD technology. This allows to close the circle between virtual and physical prototypes.
Finally, most ground transportation vehicles must be certified under impact and crash test. Optimec uses SIMULIA ABAQUS’s explicit dynamic solver to simulate impact and crash cases as specified by several FMVSS (or other) standards.