Since 2006, Endurica has been the key software for rubber fatigue analysis. Endurica software puts engineers in control of their rubber durability at an early development stage. It helps to conceive better products and prevent engaging cost related to multiple prototypes’ creations. It lets engineers do more iterations faster, without increasing their budgets. It is the world best software for elastomers fatigue analysis.
Moreover, Endurica’s Fatigue property mapping service offers a comprehensive inventory of the fatigue properties of your material. It is going to tell your engineering team about your material’s fatigue performance capabilities.
Don’t wait to save money and predict your material comportment with Endurica. Instead of spending money into the conception of a prototype for testing, which won’t be accurate, use Endurica. It will let you know how your product interact through its lifecycle. Envision problems before even conceiving the first version of the product. Get results into hours and do as many design cycles as you want to.
Endurica capabilities are available as a stand-alone suite of tools, or integrated in FE-SAFE/Rubber.
Endurica
Benefits
- Predict your part comportment: Figure out where it might crack, how long it would last, what impacts and damages your prototype
- Optimize more: Quickly see changes into your material behavior, part geometry, or load history
- Competitive advantage: Understand and communicate durability issues with realistic results
- Faster go-to-market: Save time and cost while reducing physical prototypes.
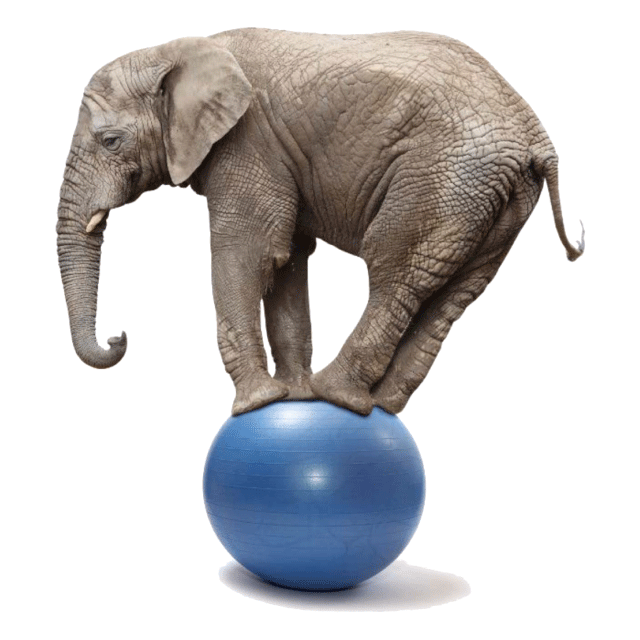
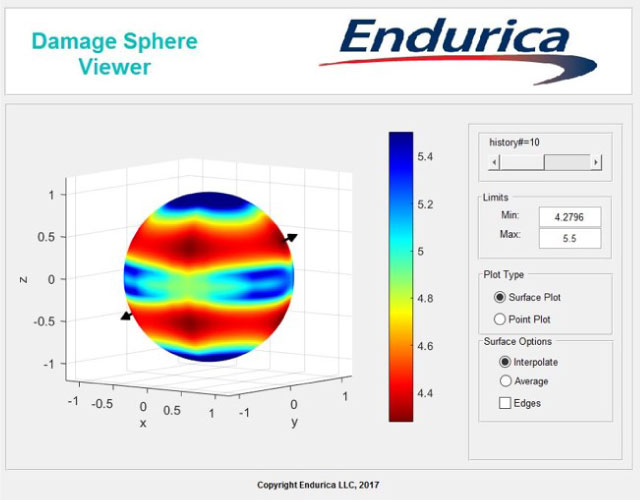
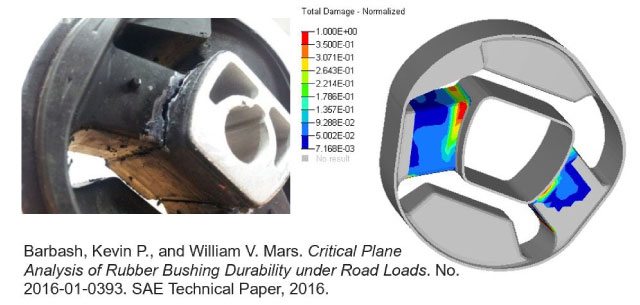
Endurica
Features
Endurica is compatible with the best simulation software such as ABAQUS and MSC MARC, giving flexibility and easing the analysis process.
Additionally, Endurica offers several fatigue analysis workflows with different complexity levels depending on time and budget restrictions. From simple to complex:
- The Infinite Life approach is by far the simplest approach. Here, we say that damage will not be allowed at all. All locations in the part must operate, always, below the fatigue limit of the rubber. The required material testing is minimal, but it’s not possible to answer how long the part may last. The focus is on whether the part can have an infinite life.
- In the Safe Life approach, the chief concern is whether the part’s estimated finite life is adequate relative to the target life. Various “special effects” that govern the crack growth rate law must be quantified. Finite fatigue life is then calculated with regard to the required load cases.
- The Damage Tolerant approach acknowledges that the risk of failure always exists and therefore should be actively monitored. This approach monitors damage development via inspection and via tracking of accrued damage under actual loading history. Remaining residual life is calculated given the actual loading history to date.
- The Fall-Safe approach takes for granted that failure is going to occur, and obliges the designer to implement measures that allow for this to happen safely. This can take several forms, such as mechanical fuse, weak link or life monitoring.